Types of Metal Finishing
Metal finishing is used to treat the exterior of a metal product by applying a thin complementary layer to its surface. There are numerous types of metal finishing processes that can be used for a variety of purposes. In this guide, we will review the major finishing methods, as well as applications and considerations for choosing a metal finishing process. Some of the general advantages of applying this finishing treatment to a metal product include:
- Increased durability
- Improved decorative appeal
- Enhanced electrical conductivity
- Higher electrical resistance
- Higher chemical resistance
- Higher tarnish resistance
- Potential for vulcanization
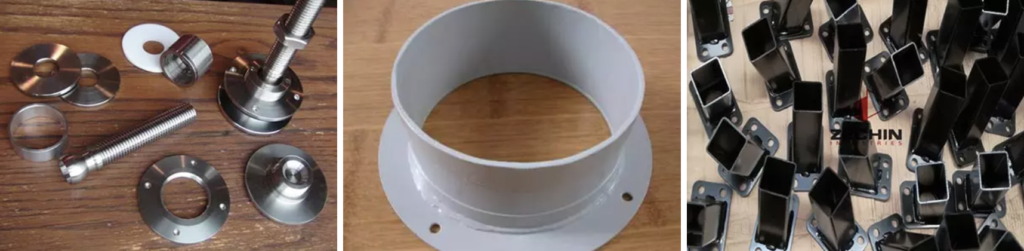
Types of Metal Finishing
- HDG (Hot Dip Galvanising) / Metal Plating
- Powder Coating
- Aluminium Anodizing
- Duplex Coating
- Industrial Paint
Metal Plating
Metal plating machines use a chemical bath to coat or alter the surface of a substrate with a thin layer of metal, such as nickel, Zinc. The electroplating method generates an electric current to coat the substrate, while electroless plating employs an autocatalytic process in which the substrate catalyzes the reaction.
Metal plating provides a number of advantages as a finishing process. It can improve a product’s durability, corrosion resistance, surface friction, and exterior appearance. It is also a useful option for coating other metals. In high-volume production runs, a barrel-finishing machine is a fast and efficient plating solution. However, plating machines are generally not suited for smoothing out surface
Powder Coating
Powder coating applies a decorative finish that is like paint, but with greater durability. The process involves melting dry plastic powder onto the metal to produce a textured, matte, or glossy coating. A textured powder- coating machine is also highly effective in removing surface defects.
Aluminum Anodizing
An electrolytic passivation process used to increase the thickness of the natural oxide layer on the surface of aluminum parts. There are three types of anodizing (Type I, Type II, and Type III) which use different acids to create the anodize coating.
- Function
- Increase wear resistance
- Increase corrosion resistance
- Prevents galling of threaded components
- Increase adhesion for paint and primers
- Increase surface hardness
Duplex coating
A duplex coating is defined as a combination of two different coating systems which often complement one another. Typically, this means a metallic coating overcoated by an organic system. Examples of such systems are hot dip galvanizing surfaces which have been painted or powder coated.